Imagine a syringe with the tip sealed. If you try to push the plunger, you’ll encounter significant resistance because the air (or liquid, if filled) inside is compressed.
A hydraulic lock works on the same principle, but with much higher pressures and specifically designed components. Let’s delve into the workings of hydraulic locks, focusing on their mechanism, principles, and applications.
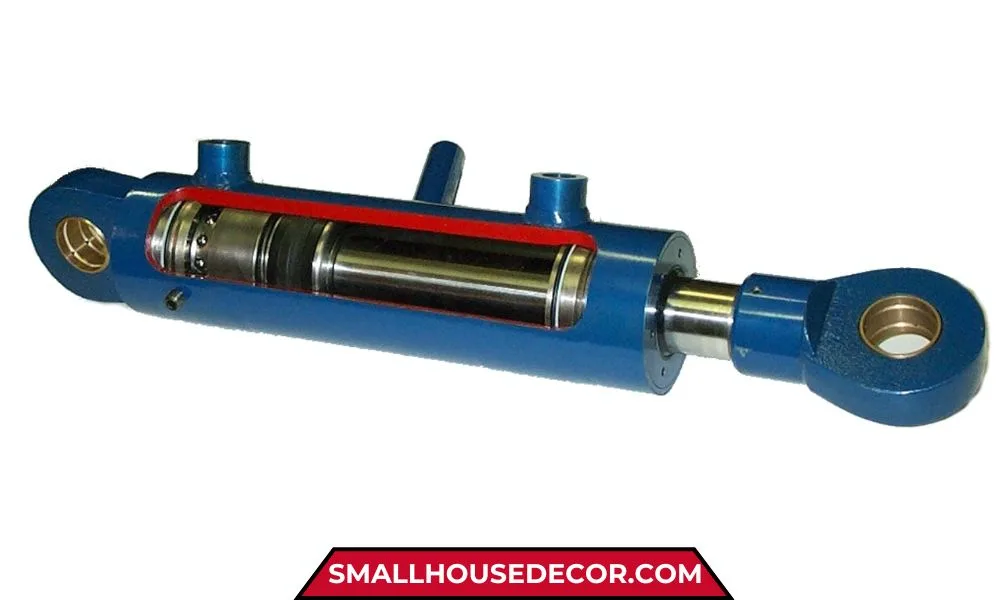
Core Principle: Incompressibility of Fluids
Hydraulic systems, including hydraulic locks, operate based on Pascal’s Law, which states that pressure applied to an enclosed fluid is transmitted undiminished to every part of the fluid and the walls of its container.
Crucially, liquids (like hydraulic oil) are nearly incompressible. This incompressibility is the foundation of how hydraulic locks function.
How Hydraulic Pressure is Stored in a Hydraulic Lock
Components:
Cylinder and Piston: The core of a hydraulic lock comprises a cylinder and a precisely fitted piston. This piston connects to the component that needs to be secured in place, such as a crane arm or a press ram.
Valves: One or more valves are employed to control the hydraulic fluid’s flow into and out of the cylinder. These valves are essential for the locking mechanism to function properly.
Locking Mechanism:
Trapping the Fluid: To engage the lock, the valves are shut, trapping a specific amount of hydraulic fluid within the cylinder.
Incompressibility Principle: Since hydraulic fluid is practically incompressible, any attempt to move the piston encounters significant resistance due to the pressure surge within the trapped fluid. This pressure buildup essentially creates a solid barrier, preventing movement.
Additional Points:
- The force exerted by the lock is directly proportional to the trapped fluid’s surface area and the pressure acting on it. A larger surface area or higher pressure translates to a more robust locking force.
- Hydraulic locks offer several advantages, including simplicity, reliability, and the ability to generate high locking forces without complex mechanisms.
- They are widely used in various applications, such as construction equipment, machine tools, and material handling systems.
I hope this explanation clarifies how hydraulic pressure is stored and utilized in a hydraulic lock.
Also Read: Wondering how traditional locking mechanisms compare? Learn more about mechanical locks and their role in securing homes and businesses.
In-Depth Explanation of the Hydraulic Lock Working Principle
Hydraulic locks play a vital role in various machinery and systems by preventing unintended movement and ensuring stability. They achieve this by utilizing the incompressibility of hydraulic fluid and precisely controlled valves.
Their primary functions can be categorized as:
Normal Operation (Movement):
In normal operation, the hydraulic system functions as intended. Hydraulic fluid is pumped into the cylinder, causing the piston to move. This movement is controlled by valves that direct the fluid flow.
Typically, a directional control valve (DCV) is used to control the direction of piston movement (extension or retraction). When the DCV is in an open position, fluid can flow freely between the pump, cylinder, and reservoir, allowing for normal operation.
Locking
To engage the hydraulic lock, one or more valves are closed, trapping the hydraulic fluid within the cylinder. This creates a “hydraulic block” because the trapped fluid cannot be compressed, preventing any movement of the piston. Several valve configurations can achieve this:
- Check valves: These valves allow flow in only one direction. By strategically placing check valves, fluid can flow into the cylinder to extend or retract the piston, but it cannot flow back out, effectively locking the piston in place.
- Pilot-operated check valves: These valves are similar to check valves but can be opened by a pilot pressure signal. This allows for more controlled locking and unlocking.
- Directional control valves (DCVs): Some DCVs have a “center” or “closed” position that blocks flow in both directions, effectively locking the cylinder.
Unlocking
To release the lock and allow movement, the valve(s) that trapped the fluid are opened. This allows the fluid to flow out of the cylinder (or into the other side of the cylinder for movement in the opposite direction), enabling the piston to move freely again. This is achieved by:
- Reversing the flow through a DCV: Shifting the valve to a position that allows fluid to flow out of the cylinder.
- Applying pilot pressure to a pilot-operated check valve: This opens the valve, allowing fluid to flow out.
Key Components Involved:
The operation of a hydraulic lock relies on a few key components:
- Hydraulic Cylinder: The actuator that converts hydraulic pressure into linear motion.
- Piston: The component within the cylinder that moves in response to hydraulic pressure.
- Hydraulic Fluid: An incompressible fluid (typically oil) that transmits force within the system.
- Valves: Precisely controlled valves that regulate the flow of hydraulic fluid into and out of the cylinder. These are the key to the locking mechanism. Common types include:
- Directional control valves: Direct the flow of fluid to control the movement of the piston.
- Check valves: Allow fluid flow in only one direction, preventing backflow and maintaining pressure.
- Pilot-operated check valves: Check valves that can be opened by a pilot pressure signal, allowing controlled release of the lock.
Hydraulic Locks Real World Applications
Hydraulic locks function is to create an immovable barrier within the hydraulic system, effectively “freezing” the position of a cylinder or actuator. This is crucial for several reasons:
Holding Position
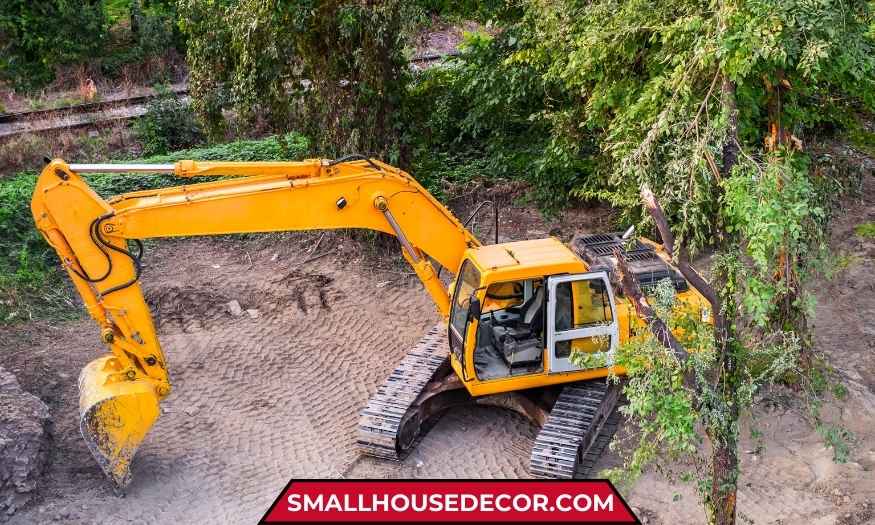
This is perhaps the most common application. Imagine a crane lifting a heavy load. A hydraulic lock ensures the boom remains at the desired angle, preventing it from drooping or shifting due to the weight. This is vital in applications requiring precise positioning, such as:
- Construction equipment: Excavators, backhoes, and cranes rely on hydraulic locks to maintain arm and bucket positions during operation.
- Manufacturing machinery: In robotic arms or automated assembly lines, hydraulic locks hold components in place during processing.
- Aircraft landing gear: Hydraulic locks secure the landing gear in the deployed or retracted position during flight.
Stability
In dynamic situations involving varying loads or external forces, hydraulic locks ensure stability by preventing oscillations or unwanted movement. This is particularly important in:
- Off-road vehicles: Hydraulic locks in suspension systems can help maintain stability on uneven terrain.
- Marine applications: Stabilizing platforms or equipment on ships in rough seas.
- Industrial robots: Maintaining stability during high-speed movements and precise manipulations.
Safety
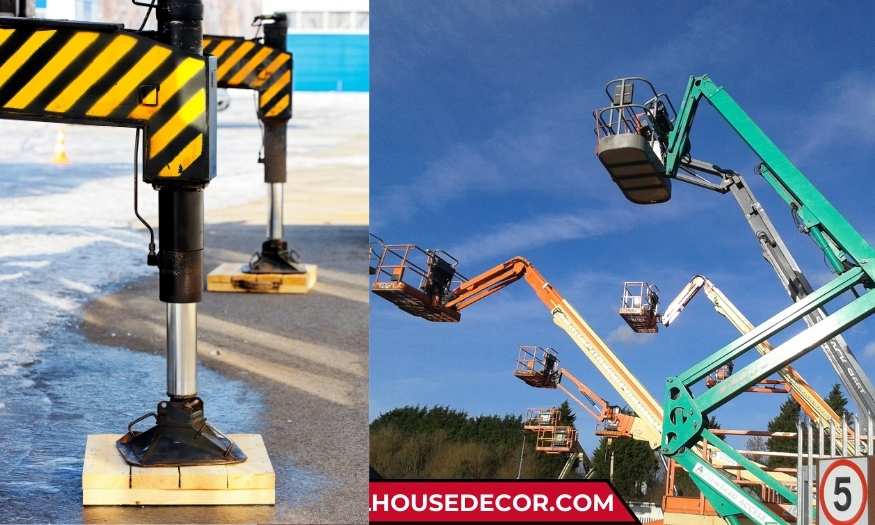
Accidental movement of heavy machinery or components can lead to serious injuries or damage. Hydraulic locks provide a crucial safety measure by preventing such incidents. Examples include:
- Stabilizing lifting platforms: Preventing sudden drops or shifts that could endanger workers.
- Securing machine tools: Preventing unintended movement of cutting tools or workpieces during operation.
- Emergency stops: In some systems, hydraulic locks can be rapidly engaged as part of an emergency stop procedure.
Applications in Residential Houses
While hydraulic locks are commonly associated with heavy machinery and industrial applications, their unique properties can also be beneficial in residential settings. Here’s an exploration of how hydraulic locks can be applied in a house:
Enhanced Security
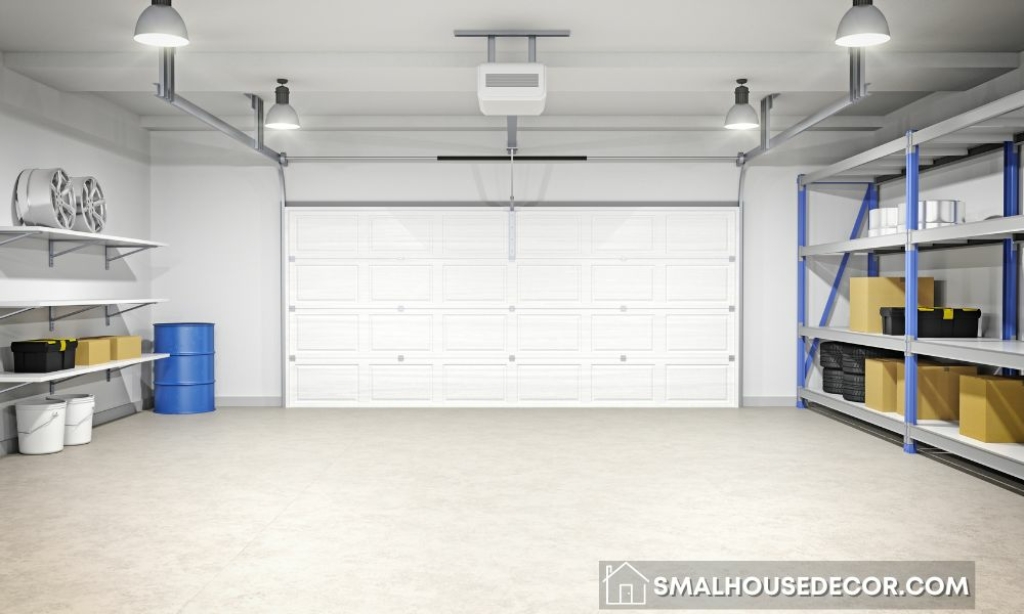
- Door and Window Locks: Hydraulic locks can provide an extra layer of security for doors and windows. Unlike traditional mechanical locks, hydraulic locks remain engaged even during power outages, ensuring continuous protection. Their resistance to tampering and forced entry is also significantly higher.
- Garage Door Security: Hydraulic locks can be integrated into garage door mechanisms to provide robust security against unauthorized access. This is especially useful for attached garages, which often serve as entry points to the main house.
Improved Home Automation
- Automated Gates: For homes with automated gates, hydraulic locks can ensure the gate remains securely closed when needed, preventing unwanted entry. They can be integrated with remote control systems or smart home technology for convenient operation.
- Adjustable Furniture: Hydraulic locks can be used in adjustable furniture, such as reclining chairs or murphy beds, to provide smooth and secure position locking. This allows for precise adjustments and prevents sudden movements.
Safety Features
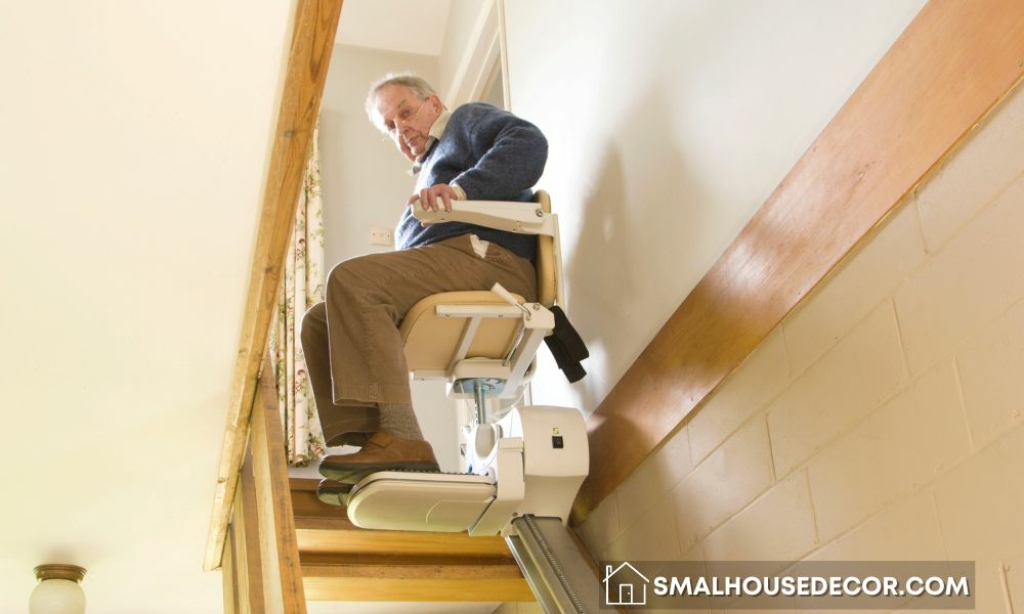
- Stairlifts and Elevators: Hydraulic locks are crucial safety components in stairlifts and residential elevators. They ensure the platform remains securely in place during entry and exit, preventing accidents. In case of power failure, the hydraulic lock engages automatically, preventing uncontrolled movement.
- Child Safety: Hydraulic locks can be incorporated into child safety mechanisms, such as gates for stairways or safety covers for potentially hazardous areas. Their robust locking capability provides an effective barrier for young children.
Other Potential Applications
- Securing Valuables: Small-scale hydraulic locks could be used in home safes or jewelry boxes to provide enhanced security for valuable possessions.
- Tool and Equipment Storage: Hydraulic locks can be used to secure storage cabinets or toolboxes in garages or workshops, preventing theft and ensuring tools remain organized.
Benefits of Using Hydraulic Locks in a House
- High Security: Hydraulic locks offer superior resistance to forced entry compared to traditional mechanical locks.
- Reliability: They are designed for heavy-duty applications and are known for their reliability and long lifespan.
- Power Outage Security: Unlike electronic locks, hydraulic locks remain engaged even during power outages.
- Smooth and Controlled Movement: They provide smooth and controlled movement in applications such as adjustable furniture or automated gates.
Considerations
- Cost: Hydraulic locking systems can be more expensive than traditional locking mechanisms.
- Complexity: Installation and maintenance may require specialized knowledge.
- Size: Depending on the application, hydraulic components may be larger than traditional counterparts.
While hydraulic locks might not be a common feature in most homes today, their unique advantages in security, automation, and safety make them a viable option for homeowners looking for enhanced performance and reliability. As technology advances and costs potentially decrease, we may see more innovative applications of hydraulic locks in residential settings in the future.
Types of Hydraulic Locks
Hydraulic locks are essential components in hydraulic systems that prevent unwanted movement or backflow of fluid, effectively “locking” a cylinder or actuator in place. Here are the main types:
Simple Check Valve Lock
This is the most basic type of hydraulic lock. It utilizes a simple check valve, which is a one-way valve that allows fluid to flow in only one direction.
How it works: When hydraulic pressure is applied in the allowed direction, the check valve opens, allowing fluid to pass through and actuate the cylinder. When the pressure is removed or tries to reverse, the check valve closes, preventing backflow and locking the cylinder in its current position.
- Advantages: Simple, inexpensive, and reliable.
- Disadvantages: Offers limited control and may not be suitable for high-precision or safety-critical applications.
Pilot-Operated Check Valve Lock
This type of lock uses a more sophisticated check valve that requires a pilot pressure signal to open and allow flow in both directions.
How it works: When pilot pressure is applied, it overrides the check valve’s spring force, allowing fluid to flow freely in either direction. When the pilot pressure is removed, the check valve acts like a simple check valve, preventing backflow and locking the cylinder.
- Advantages: Provides more controlled locking and unlocking, higher safety, and can be integrated into more complex hydraulic circuits.
- Disadvantages: More complex and expensive than simple check valves.
Counterbalance Valves
These valves are specifically designed to control overrunning loads, which are loads that tend to move due to gravity or other external forces.
How it works: Counterbalance valves are typically installed on the rod side of a cylinder and create back pressure to resist the load’s tendency to move. This back pressure is proportional to the load, providing a controlled descent and preventing the load from “running away.”
- Advantages: Provides smooth and controlled movement of overrunning loads, prevents cavitation, and can also function as a hydraulic lock when the load is stationary.
- Disadvantages: More complex and expensive than simple check valves, requires careful tuning to match the specific load and application.
Additional Notes:
- Hydraulic locks are essential for safety in many applications, such as holding heavy loads in cranes or preventing unintended movement in machinery.
- The choice of hydraulic lock depends on the specific application requirements, such as the load, speed, precision, and safety considerations.
- In some cases, a combination of different types of hydraulic locks may be used to achieve the desired performance.
Common Issues in Hydraulic Locks and How to Troubleshoot Them
Like any mechanical system, hydraulic locks can experience issues that affect their performance. Here are some common problems and troubleshooting tips:
1. Failure to Lock
- Possible Causes:
- Contamination: Dirt, debris, or other contaminants can prevent the check valve from seating properly, allowing backflow.
- Worn or Damaged Seals: Worn or damaged seals in the check valve or cylinder can cause internal leakage, preventing the lock from holding pressure.
- Mechanical Failure: Springs, poppets, or other internal components of the check valve may be broken or malfunctioning.
- Troubleshooting Steps:
- Inspect for Contamination: Check for dirt or debris around the check valve and clean as necessary.
- Check for Leaks: Look for external leaks around the check valve and cylinder. If leaks are present, replace the affected seals.
- Test the Check Valve: If possible, test the check valve for proper function. Replace the valve if it is not working correctly.
2. Failure to Unlock
- Possible Causes:
- Insufficient Pilot Pressure: In pilot-operated check valves, insufficient pilot pressure may prevent the valve from opening.
- Pilot Line Blockage: A blockage in the pilot line can prevent the pilot pressure from reaching the valve.
- Mechanical Binding: Internal components of the check valve may be binding or stuck.
- Troubleshooting Steps:
- Check Pilot Pressure: Verify that the pilot pressure is within the specified range.
- Inspect Pilot Lines: Check for kinks, blockages, or leaks in the pilot lines.
- Manually Override (If Possible): Some pilot-operated check valves have a manual override that can be used to open the valve. If this works, it indicates a problem with the pilot pressure system.
3. Leakage
- Possible Causes:
- Worn or Damaged Seals: As mentioned earlier, worn or damaged seals are a common cause of leaks.
- Loose Fittings: Loose fittings or connections can also cause external leaks.
- Cracked Housings: In some cases, the valve housing itself may be cracked or damaged.
- Troubleshooting Steps:
- Inspect for Leaks: Carefully inspect the check valve, cylinder, and associated lines for any signs of leakage.
- Tighten Fittings: Ensure that all fittings and connections are properly tightened.
- Replace Seals or Components: Replace any worn or damaged seals, fittings, or components.
4. Slow or Erratic Movement
- Possible Causes:
- Contamination: Contamination can restrict flow through the check valve, causing slow or erratic movement.
- Internal Damage: Internal damage to the check valve or cylinder can also cause these symptoms.
- Air in the System: Air trapped in the hydraulic system can cause jerky or inconsistent movement.
- Troubleshooting Steps:
- Check for Contamination: Inspect and clean the check valve and surrounding area.
- Bleed the System: Bleed the hydraulic system to remove any trapped air.
- Inspect Internal Components: If possible, inspect the internal components of the check valve and cylinder for damage.
General Troubleshooting Tips
- Consult the Manual: Always refer to the manufacturer’s manual for specific troubleshooting information and recommendations.
- Systematic Approach: Use a systematic approach to troubleshooting, starting with the most likely causes and working your way through the list.
- Cleanliness: Maintain cleanliness when working on hydraulic systems to prevent contamination.
- Safety Precautions: Take appropriate safety precautions when working with hydraulic systems, as they operate under high pressure.
Remember: If you are not comfortable troubleshooting hydraulic systems, it is best to consult a qualified technician.
Also Read: When working with pressurized systems, it’s important to understand related components like expansion tanks. Discover if an expansion tank is required for your water heater and how it helps regulate pressure.