Whether you are prototyping a new product or working in a production or construction company, you will likely require screws and fasteners at some point. Screws and fasteners help to join various components, such as cabinets, securely.
You may be able to get away with standard bolts and screws that can be purchased from any local hardware store, depending on your application. But for more specialized applications, one may require custom fasteners specific to your application.
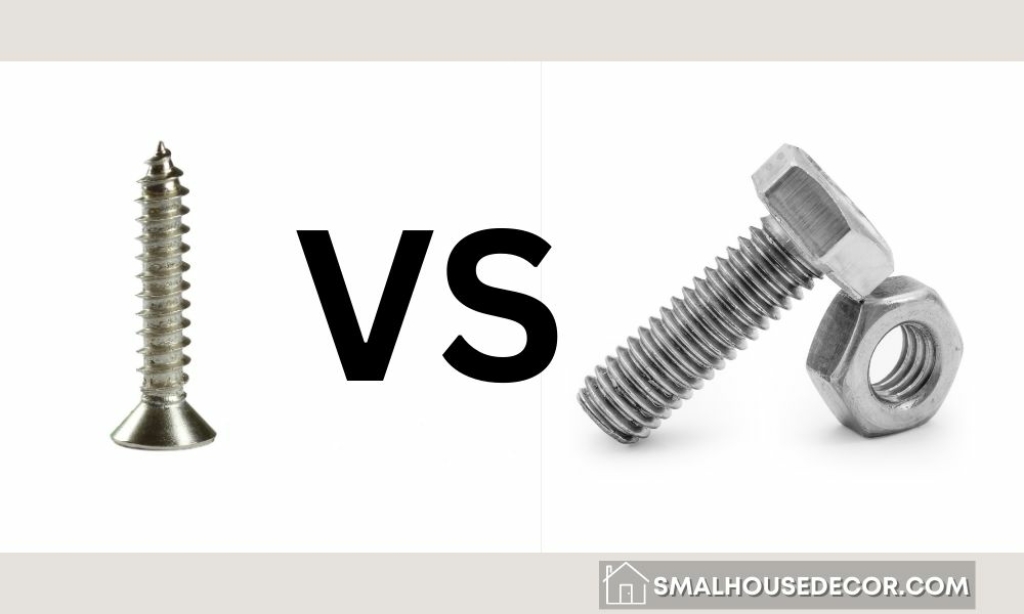
Bolts and Screws: Do They Have a Difference?
Bolts and screws include the most common types of fasteners. While bolts and screws have similarities in their outlook, they are not the same. They have a few but easy-to-identify differences.
Among the main differences between bolts and screws is that bolts require a washer and a nut on the other side of the material to fasten components. In contrast, a screw fastens directly to the material’s surface. This means that for a screw, you will only need one item alone.
Another significant difference between the two is the tools required to install them. Even though screws include various head types like square recess heads, Phillips and slotted, you will only need a drill bit for the screwdriver to insert the screw.
On the other hand, installing bolts is different. To fasten components using bolts and nuts, you must have a driver or wrench to tighten the bolt and another wrench to apply torque to the nut. In other cases, washers will be required to distribute the load of the fastener evenly.
Also Read: Curious about different lock types? See how mechanical locks work rely on proper fasteners for optimal performance and longevity.
Metals Commonly Used to Manufacture Screws
Generally, screws are made from various alloys and metals. Your application will significantly influence certain requirements, such as corrosion resistance and strength.
Aluminum
Aluminium involves a lightweight metal usually used in manufacturing custom fasteners. When compared to steel, aluminium is less durable. Nevertheless, it works perfectly in binding lighter components for different applications. This is your go-to option if you require special requirements like avoiding magnetism.
Steel
Steel is the most common metal material for manufacturing screws, following its durability and availability. Steel comes in four major types, including:
- Medium Carbon Steel- has mid-level strength and is perfect for automotive parts.
- Alloy Steel- facilitates exceptional strength and is best for socket head products.
- Stainless Steel- this varies in corrosion resistance and strength properties and has a wide selection of applications.
- Low Carbon Steel-this is ideal for automotive manufacturing, medical device manufacturing and machine manufacturing. However, it lags in durability when compared to other steel options.
Titanium
Titanium is the most durable material for fasteners and screws. Titanium screws are popular in heavy-duty applications such as the aerospace industry. Also, these screws are utilized as bone screws.
Brass
Brass is a copper-based alloy whose screws are easy to manufacture. However, this material has poor strength and rust resistance compared to other metals. Nevertheless, brass offers a cosmetic appeal commonly used in marine applications.
The most commonly used screw types include sheet metal screws, drywall screws and wood screws.
Remember that various screw types exist in general and specialized classifications. Consider your job site needs to select the most appropriate screw. Also, always buy screws from reputable dealers.